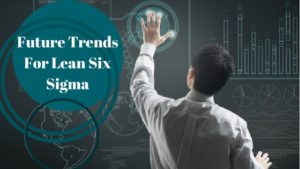
Future Trends for Lean Six Sigma
By Harry Rever, MBA, PMP, CSSMBB, CQM, CQC
If there is one commonality among businesses in virtually every industry, it is the desire to improve results.
By Harry Rever, MBA, PMP, CSSMBB, CQM, CQC
If there is one commonality among businesses in virtually every industry, it is the desire to improve results.
By Harry Rever
Is becoming a certified Lean Six Sigma Black Belt something you should consider?
By Anne Foley
I can still remember the first time I heard the term Six Sigma. Our customer invited us to a supplier meeting in the hopes of creating excitement around a new initiative they were implementing.
By Anne Foley
Let me begin by saying that if you have started a diet, this story might help you stick to it.
By Anne Foley
Lean Six Sigma is a methodology that focuses on improving business performance, reducing costs, and increasing efficiency and productivity.
Courses
Online Conferences
International Institute for Learning
485 Madison Avenue, 13th Floor
New York, NY 10022-5803
+1 (212) 758-0177
+1 (800) 325-1533
Questions and Inquiries: learning@iil.com
Tech Support:
help@iil.com
Virtual Learning Support:
+1 (212) 515-5100
Administration/Production:
+1-(212) 515-5074
© 2025 International Institute for Learning. All rights reserved.