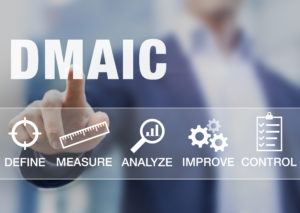
Applying the DMAIC Steps for Project Management Process Improvement
By Harry Rever, MBA, PMP, CSSMBB, CQM, CQC
“Define, Measure, Analyze, Improve, Control” is the Roadmap to Improving Processes.
By Harry Rever, MBA, PMP, CSSMBB, CQM, CQC
“Define, Measure, Analyze, Improve, Control” is the Roadmap to Improving Processes.
By Anne Foley
Let me begin by saying that if you have started a diet, this story might help you stick to it.
By Anne Foley
Here are 5 concepts from the Lean Six Sigma framework that will help you to reap the harvest you need.
Courses
Online Conferences
International Institute for Learning
485 Madison Avenue, 13th Floor
New York, NY 10022-5803
+1 (212) 758-0177
+1 (800) 325-1533
Questions and Inquiries: learning@iil.com
Tech Support:
help@iil.com
Virtual Learning Support:
+1 (212) 515-5100
Administration/Production:
+1-(212) 515-5074
© 2025 International Institute for Learning. All rights reserved.